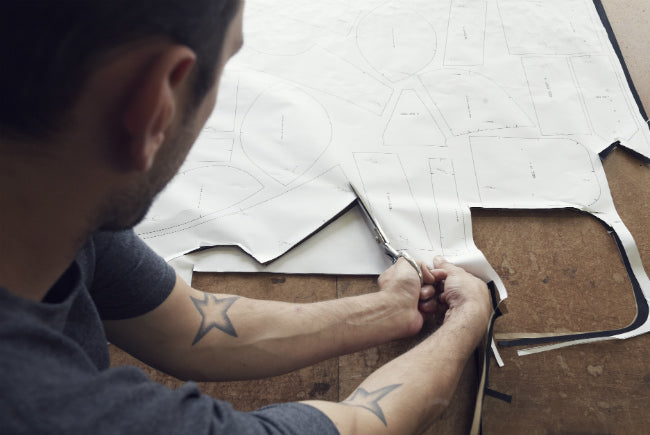
How it's Made: The Union Garage Robinson Jacket
After four months, four prototypes, a couple hundred emails and two separate 200-mile trips to Vanson’s factory in Fall River, Massachusetts, the new Robinson jacket is now in production, being made by hand—several sets of hands—one jacket at a time.
David Botelho has been working at Vanson for 17 years. As a cutter, he’s responsible for delivering each of the jacket’s many pattern pieces. He wields heavy, deadly sharp left-handed scissors with speed and accuracy.
From there it goes to the sewers, many of whom have decades of experience. They must follow an extra-long list of steps to get the Robinson jacket just right. The standard waxed cotton jacket our new jacket is based off is made up of 37 pattern piece. The Robinson recipe calls for 82 different pieces. And the production can be pain-staking.
More than just the 10.10 ounce Martexin waxed cotton, the recipe for the Robinson is made up of a medley of materials: leather along the interior facing and under the shoulder and elbow caps; thin Velcro strips sewn into said caps to hold the armor; elastic carriers to fit the armor inside the jacket, plastic surgical rivets to adhere the elastic to the D3O armor, smooth and strong sateen sleeve liners; and bright red plaid interior to give the jacket some pop.
When it’s all said and done the finished jacket doesn’t only have twice the pattern pieces as the plain cotton jacket it’s based off of—it physically weighs twice as much, too. And when it comes to functioning as a modern-day motorcycle jacket, we're confident the Robinson beats out all the other waxed cotton contenders. It's more comfortable, more practical and more protective than any other jacket in its class.



